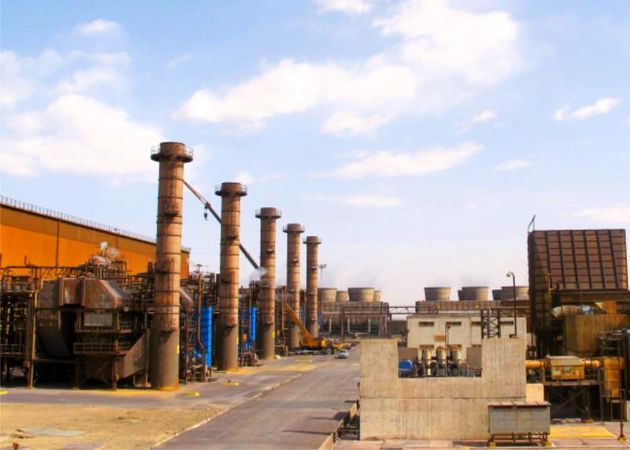
تولید فولاد با کمترین میزان مصرف انرژی و حرکت در مسیر فولاد سبز دو مقولهای است که در امر تولید فولاد به هم پیوند خوردهاند و خوشبختانه از این منظر، اراده فولاد مبارکه بر مبنای تولید بیشتر با مصرف کمتر انرژی و حرکت شتابان بهسوی تبدیلشدن به الگوی جهانی در کمترین میزان مصرف انرژی استوار است.
به گزارش مرور نیوز، سید امیر طباطبائیان، مدیر انرژی و سیالات فولاد مبارکه، با بیان این مطلب به تشریح میزان مصارف انرژی و اقدامات فولاد مبارکه در این راستا اشاره کرده که باهم پی میگیریم.
عمدهترین روشهای تولید فولاد در جهان
در دنیا دو روش عمده جهت تولید فولاد وجود دارد: یکی روش کوره بلند و استفاده از انرژی زغالسنگ فراوریشده (کک) که 70 درصد فولادسازیهای دنیا از این روش استفاده میکنند و دیگری روش احیا مستقیم و کورههای قوس الکتریکی که در فولاد مبارکه از روش دوم استفاده میشود. ازآنجاکه دسترسی به گاز طبیعی بهعنوان یک منبع انرژی پاک در همه جای دنیا وجود ندارد، عمده صنایع تولیدکننده فولاد به سمت استفاده از روش کوره بلند رفتهاند که بهدلیل انتشار دیاکسید کربن که یک گاز گلخانهای است، این روش آلودگیهای خیلی زیادی به همراه دارد.در روش دوم و با استفاده از انرژی گاز طبیعی، فولادِ بهمراتب پاکتری نسبت به روش کوره بلند تولید میشود. بهدلیل وجود مزیت گاز طبیعی بیش از 70 درصد فولادسازیهای کشور از روش کورههای احیا مستقیم و کورههای قوس الکتریکی استفاده میکنند.
انرژی مصرفی در کشور ما و در دنیا دقیقا روبهروی هم هستند، اما اهمیت وجود انرژی برای هر دو فرایند کاملا مشهود است و اگر انرژی نتواند برای تولید فولاد تأمین شود، این صنعت دچار رکود و توقف میشود. مسئله استفاده از سوخت پاک یا همان گاز طبیعی باعث میشود انتشار گاز دیاکسید کربن نصف روش کوره بلند باشد.
مقایسه میزان مصارف در برخی فولادسازیهای جهان
استفاده از سوخت پاک گاز طبیعی تولید کربن بسیار کمتری نسبت به روش کوره بلند دارد. پس اینکه عنوان میکنیم در ایران از روش پاک و بهتری برای تولید فولاد استفاده میکنیم به همین دلیل است. در دنیا هم کشورهایی که منابع گاز ارزان یا منابع سرشار گاز داشته باشند این روش ارجحیت دارد، چون این روش هم ارزان است و هم دوستدار محیطزیست و درعینحال روش ایدئالی برای تولید فولاد است. کشورهایی که در این زمینه بیشتر کارکردهاند آمریکا و مکزیک هستند که به خاطر وجود منابع گاز از این روش استفاده میکنند.
برای مصرف انرژی یک شاخص جهانی تعریف شده است. این شاخص همه روشهای تولید فولاد را باهم همسنگ میکند، یعنی نمیتوانیم بگوییم چون روش تولید فولاد در ایران استفاده از احیا مستقیم است، مصرف انرژی برق بیشتر از روش کشورهایی است که قوس الکتریکی ندارند. این حرف اشتباه است، چون در کشور ما از انرژی الکتریکی و در فرایند کوره بلند از انرژی زغالسنگ استفاده میشود. بنابراین واحد مشترکی تعریف شده که نشان میدهد به ازای هر تن فولاد چند گیگاژول انرژی مصرف شده است. این واحد زبان مشترکی است بین تمام فرایندهای تولید و ما بر اساس این شاخص میتوانیم بگوییم میزان مصرف انرژی ما خوب است یا بد.
در فولاد مبارکه مصرف انرژی به ازای تولید تختال نزدیک 22.9 گیگاژول بر تن اسلب است. البته این عدد ممکن است به دلیل محدودیتهایی که وجود دارد، در فصول مختلف متفاوت باشد. در دنیا هم این اعداد متفاوت است؛ مثلا در انگلستان 18.5 گیگاژول بر تن اسلب و در آمریکا 23 گیگاژول بر تن اسلب، در هند 27 و اوکراین 29 و در شرکتهای فولادساز ژاپنی اعداد کمتر است.
بهطورکلی میزان مصرف انرژی فولاد مبارکه مطابق با استانداردهای جهانی است. اگرچه در دنیا بهترین نیستیم، ولی به سمت بهترینها در حال حرکتیم؛ این در حالی است که مصرف انرژی در شرکت هم اعداد قابل قبولی نسبت به سایر فولادسازهای جهانی به شمار میرود.
اقدامات انجامشده برای کاهش حداکثری مصارف و استفاده بهینه از منابع انرژی در فولاد مبارکه
فولاد مبارکه سال 71 تأسیس شد و در سال 77 کمیته عالی انرژی در آن ایجاد گردید. ریاست این کمیته به عهده معاونت بهرهبرداری است و معاونت تکنولوژی، مهندسی کارخانه و کل مدیران نواحی تولیدی عضو این کمیته هستند؛ ضمن اینکه دبیری کمیته را هم ناحیه انرژی و سیالات بر عهده دارد. این کمیته با این هدف ایجاد شده که بتوانیم اول از همه، انرژی موردنیاز خطوط تولید را تأمین کنیم و در مرحله بعد از بهترین و بهروزترین تکنولوژیها در روشهای تولید خود بهره ببریم تا با استفاده از روش بهینه، هم منافع اقتصادی کسب کنیم و هم میزان مصرف انرژی و آلودگی محیطزیست را به حداقل برسانیم. موضوع بعدی استقرار سیستم مدیریت انرژی است که با کمک این کمیته و اقدامات انجامشده، از سال 94 موفق شدیم استاندارد مصرف انرژی یا همان
ایزو 50001 را در شرکت پیادهسازی کنیم و هرسال این استاندارد تمدید شده است. تمدید این گواهینامه بهمنزله این است که برای مدیریت انرژی برنامهریزی میکنیم که موجب کاهش مصرف انرژی میشود.
برخی پروژههای انجامشده در راستای کاهش و بهینهسازی مصارف
طی این سالها پروژههای بسیار زیادی در این راستا انجام شده است که بهترینها آنها را میتوان تولید بخار سوپرهیت از انرژی دودکش نیروگاه گازی دانست. با اجرای این پروژه مصرف گاز طبیعی در فولاد مبارکه به میزان 12 هزار نرمال مترمکعب در ساعت کاهش یافته و این بدان معنی است که به میزان قابلتوجهی به سمت تولید فولاد سبز و تولید هرچه کمتر CO2 گام برداشتهایم. مضاف بر اینکه راندمان این نیروگاه از 30 درصد به 36 درصد رسیده که در نوع خود عدد بزرگی است.
پروژه دیگر احداث نیروگاه CHP جهت تولید همزمان برق و حرارت در مجتمع فولاد سباست که به بهرهبرداری رسیده است.علاوه بر این، پروژههای دیگری هم در نواحی مختلف فولادسازی، آهنسازی و نورد گرم و سرد اجرا شده؛ تاجاییکه در سال 1400 شرکت فولاد مبارکه موفق شد نزدیک به 4.5 میلیون گیگاژول مصرف انرژی خود را کاهش دهد.
نکته قابلتوجه این است که در این زمینه همواره پروژههای جدید و قویتری تعریف و اجرایی میشوند و این اقدامات برای کاهش مصارف ادامهدار است. ازجمله این پروژهها میتوان به توسعه ریکوپراتورهای احیا مستقیم که هم کاهش مصرف انرژی و هم افزایش میزان تولید را به همراه دارد، و پروژه احداث نیروگاه تجدیدپذیر که شرکت را با سرعت بیشتری به سمت تولید فولاد سبز سوق داده است، اشاره کرد.
به خاطر داشته باشیم احداث نیروگاه حرارتی که از طرحهای توسعه جدید فولاد مبارکه است، با راندمان حدود 60 درصد حدود 23 درصد بیشتر از متوسط راندمان نیروگاههای کشور تعریف شده است. این بدان معنی است که با مصرف همان میزان گاز میتوانیم انرژی الکتریکی بیشتری تولید کنیم.
هدفگذاری فولاد مبارکه
هدفگذاری فولاد مبارکه در کوتاهمدت و بلندمدت، کاهش حداکثری مصارف و استانداردسازی بهروز است. این شرکت همیشه بر اساس استاندارد مدیریت انرژی یا ایزو 50001 برنامه کاهش مصرف انرژی را پیگیری کرده است. بدین منظور هرساله با همکاری نواحی تولیدی، برنامه کاهش مصرف انرژی هر بخش استعلام و در ناحیه انرژی و سیالات برای اجرای آنها پروژههایی تعریف میشود. پروژهها بعد از ارزیابی اقتصادی و اخذ تأییدیههای لازم از کمیتههای داخلی ازجمله کمیته عالی انرژی، وارد فاز تخصیص بودجه و نهایتا اجرا میشوند.
مصرف گاز صنعت فولاد 4 تا 6 درصد انرژی مصرفی در کل کشور
در صنعت فولاد، برخلاف ذهنیتی که وجود دارد، میزان مصرف انرژی نسبت به مصرف انرژی کل کشور مقداری ناچیز است. طبق آمارهای وزارتخانههای مربوطه، مصرف گاز صنعت فولاد 4 تا 6 درصد گاز مصرفی در کل کشور است و این عدد در مقایسه با اعداد دیگر، مثلا در بخش خانگی، حملونقل، نیروگاهها، کشاورزی و تلفاتی که در شبکه وجود دارد، بسیار ناچیز است و صنعت فولاد سهم زیادی در مصرف انرژی کشور ندارد. بنابراین لازم است همه بخشها درزمینه بهینهسازی و کاهش مصرف انرژی گاز اقدام کنند. در بحث برق نیز همینطور است و تقریبا 6 تا 7 درصد برق کشور در صنعت فولاد مصرف میشود که این عدد هم نسبت به کل مصرف، عدد بزرگی نیست. درنهایت اینکه ما با سرمایهگذاری در بخشهایی که عمده مصرف انرژی را در کشور دارند میتوانیم نتایج بهتری بگیریم و چنانچه همه بخشها همکاری کنند، دیگر شاهد قطعی و یا محدودیت انرژی برای صنعت و دیگر بخشها در فصول مختلف سال نخواهیم بود.
صنعت فولاد مولد، اشتغالزا و گرداننده چرخ سایر صنایع
به خاطر داشته باشیم اگر انرژی و سوختی در اختیار صنایع قرار میگیرد، در ازای آن تولید اتفاق میافتد و ارزشافزودهای ایجاد میشود که موجب به گردش درآمدن چرخ سایر صنایع، بهبود اشتغال، جلوگیری از واردات و خامفروشی محصولات در کشور میشود. پس بهتر است سرمایهگذاریها و سیاستگذاریهای بهینهسازی مصرف انرژی به سمت بخشهای غیرمولد، یعنی جاهایی که انرژی را با شدت خیلی زیاد مصرف میکنند و تولیدی هم در قبال آن مصرف ایجاد نمیکنند، سوق داده شود.
نباید فراموش کرد که در 30 تا 40 سال اخیر، صنعت فولاد که یکی از صنایع مولد و شاخص کشور بوده است و باید با سیاستگذاری صحیح، راه پویایی هرچه بیشتر این صنعت هموار گردد تا در پی آن، شاهد رونق تولید و توسعه در سایر صنایع استراتژیک کشور باشیم.